Special tool for closure is one of the last projects we have done in METALMAQ, leaving a good lesson for future projects.
THE PROBLEM
Our customer, located in northern Spain, is a manufacturer of containers for the wine industry.
In a new container design, they wanted to stop welding tubes (the typical system used) and decided to make a completely closed part on their press brake machine, as can be seen in the following drawing:
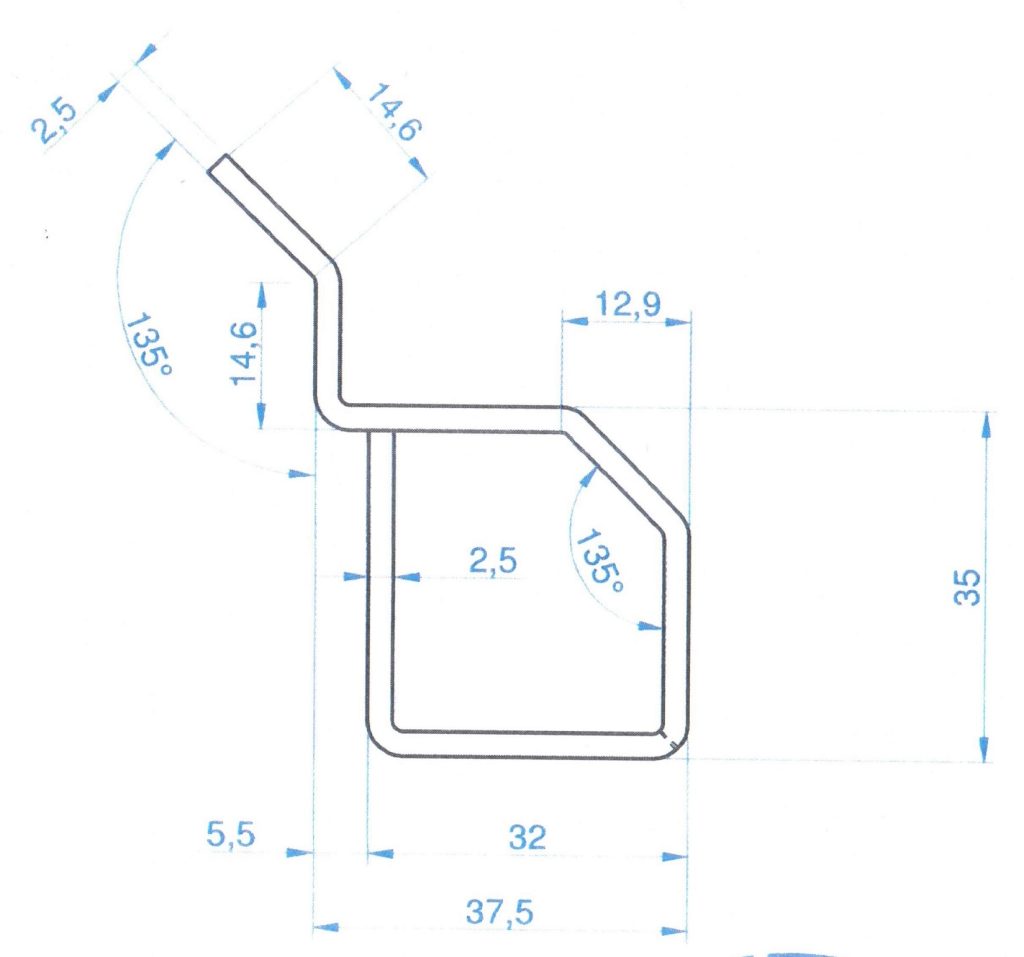
For this reason, they contacted us to see how we could manufacture a tool that could make their design on their sheet metal press brake machine.
THE SOLUTION
Our Technical Office designed a tool to make the aforementioned closure. METALMAQ has already manufactured similar tools on several occasions. They are always special tools, as each customer makes a figure with different measurements and thicknesses, so each one is different from the previous one.
Once the design has been made, it is sent to the customer for their explanation and acceptance.
Sketch of how the closure system works;
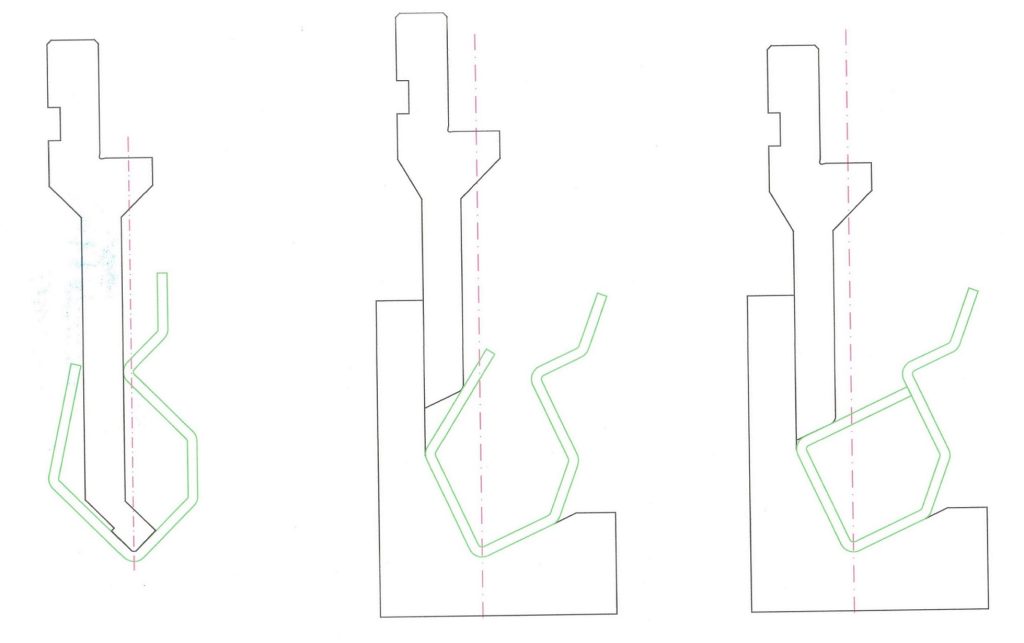
Once the first phase is completed, we start with the testing phase. A prototype is made to see the real behaviour of the part. The customer sends us samples of the sheets they are going to work with. We usually do the tests with the customer’s sheets to avoid possible bending variants. As we expected, the base of the part bulged out somewhat. This is because the last bend, as it is not made in a V of a typical die, is not supported on the sides of the sheet, causing this bending to occur at the base of the part.
We send the customer the photos of the tests, as shown in the photo below:
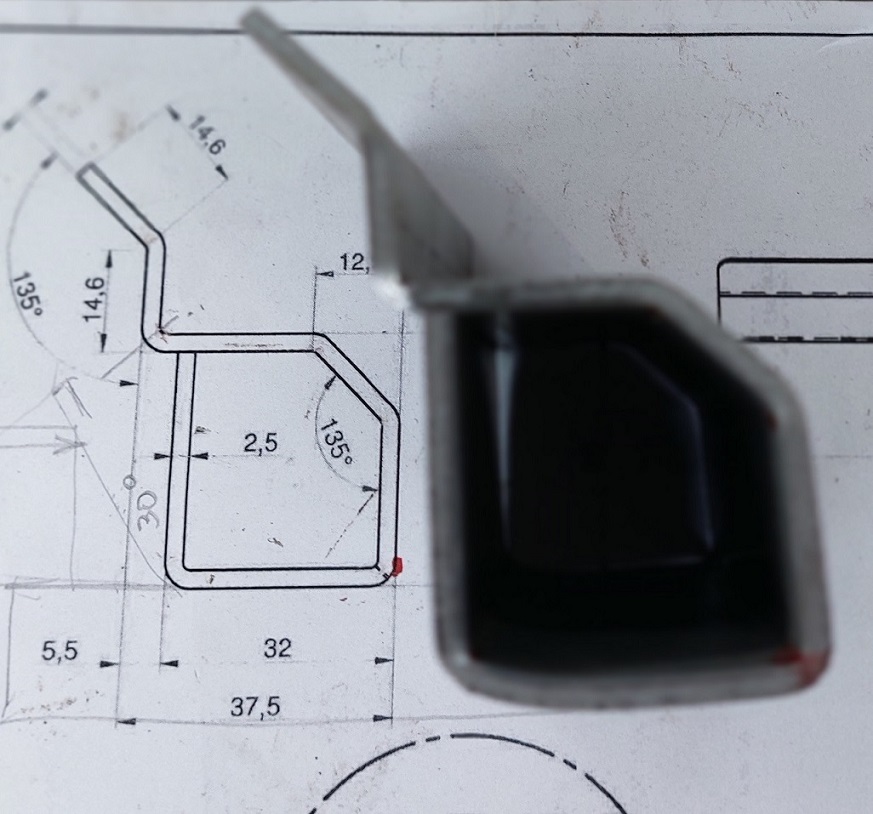
For our customer, it is of the utmost importance that there is no deformation. We ultimately found a solution: since our customer has a laser cutting system, we make some small “windows” right along the bending line of the last step. Afterwards, we do the tests and the bend is perfect.
As can be seen in the following photographs of the samples taken, the “bulging” that was generated in the first tests no longer exists.
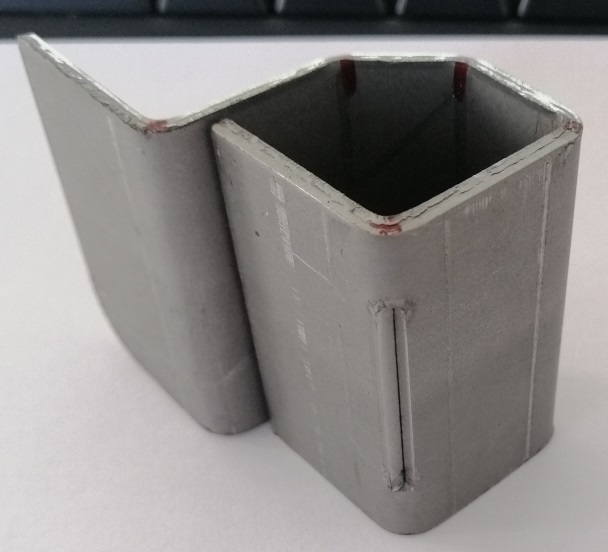
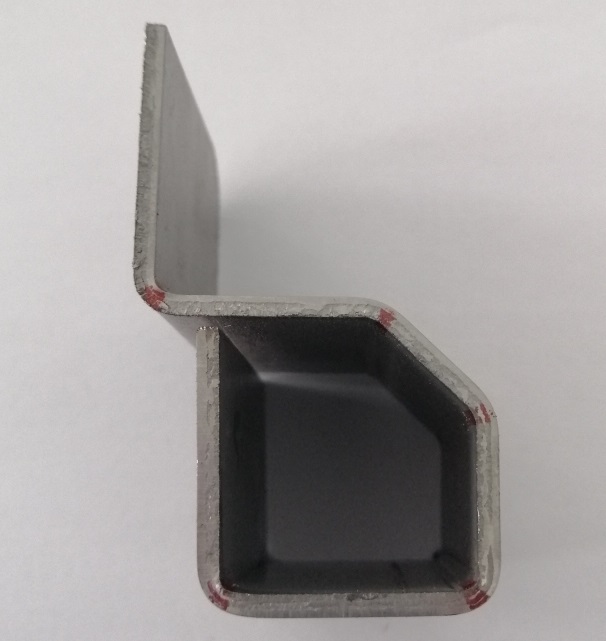
Having solved this problem, we now move on to manufacture the tools that will be used for the mass production of the bent metal parts.
MANUFACTURE
The tools are made of our standard C-50 steel, induction hardened in the working and grinding areas, so that the tool can be used on a regular basis and without premature wear due to typical use.
The clamps for both punch and die are Promecam, since our customer has an AMADA press brake, and have been manufactured in one 835 m/m section and another 415 m/m section, for a total length of 1,250 mm.
The following photographs show the entire manufactured tool (punch + die).
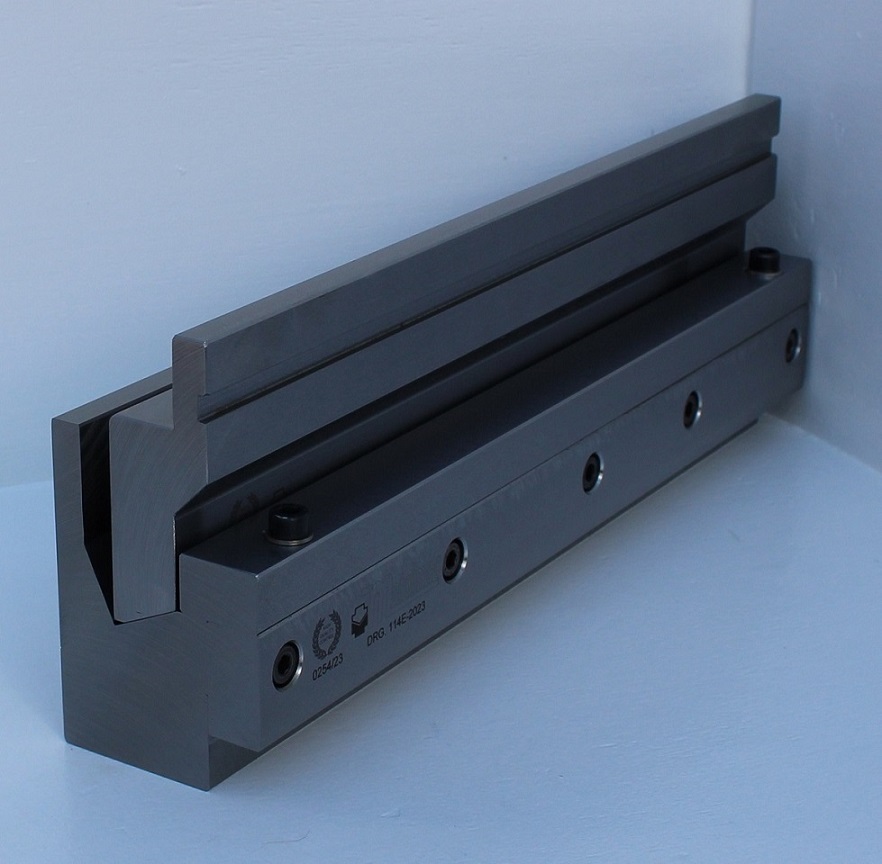
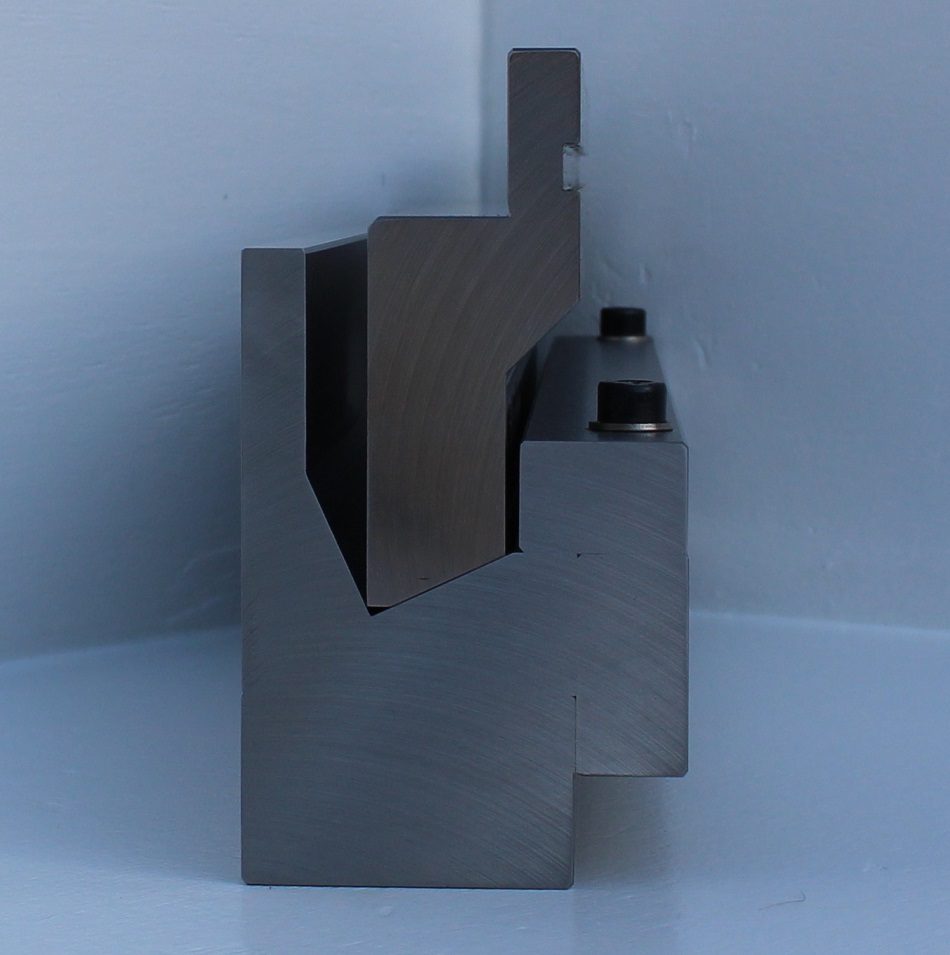
At the bottom of the tool (the die) there are some screws in the upper part. These are used to regulate the closing capacity of the part, as it is common for different batches of sheets to come with minor changes in thickness and hardness, and therefore this regulation guarantees the optimum result of the bent parts.