Das Herstellen von Laschen oder Rändern an Blechen, insbesondere Blechen mit geringeren Stärken, ist sehr häufig. Es gibt unterschiedliche Gründe für die Herstellung dieser „zusammengedrückten Knicke“, und die häufigsten sind:
– Ein besserer Abschluss der Werkstücke
– Verhindern, dass sich die Benutzer an den Blechrändern schneiden
– Verstärkung der Steifigkeit der Metallteile
ZWEI ARTEN VON „LASCHEN“
Es gibt zwei Arten von „Laschen“. Bei der ersten wird ein wenig Rundung belassen. Diese Art wird bevorzugt empfohlen, denn es werden weniger Spuren auf dem Blech hinterlassen und darüber hinaus wird zum Herstellen weniger Tonnage benötigt.
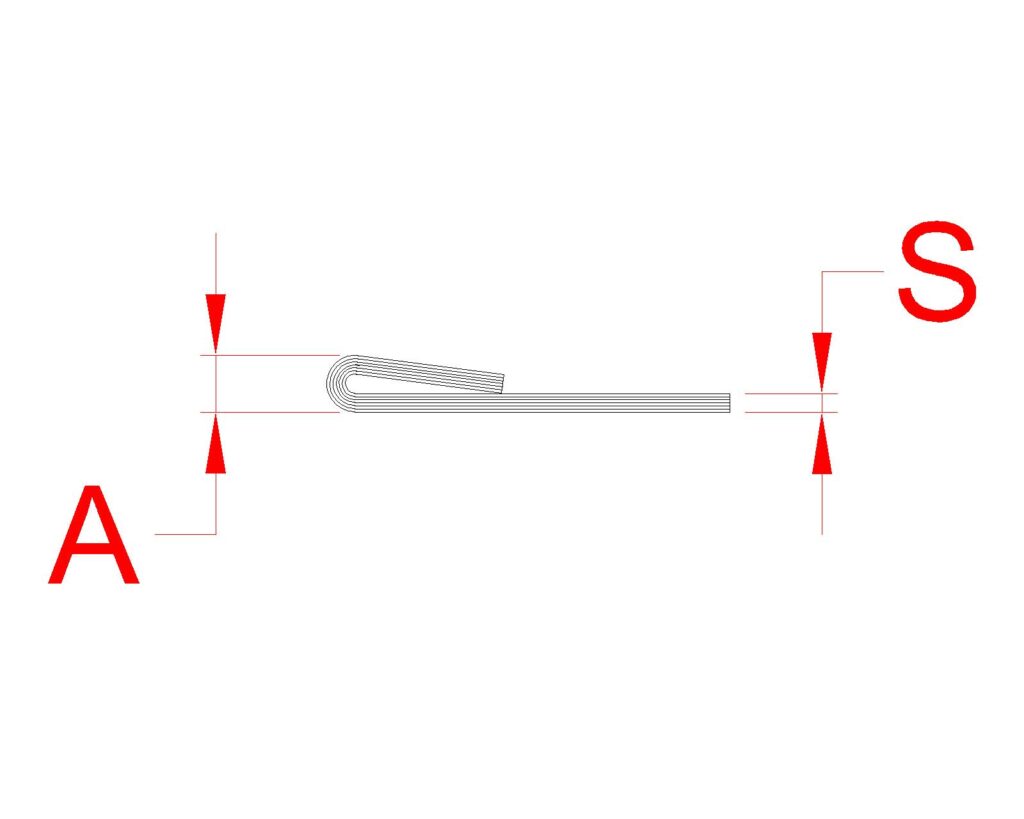
Die zweite Form ist die vollkommen zusammengedrückte Form. Diese wird üblicherweise nicht empfohlen, denn sie hinterlässt eine kleine Markierung auf dem Blech (siehe Pfeil auf der beigefügten Skizze). Diese Markierung wird durch die Spannung beim Abkanten der „Lasche“ verursacht. Dabei entsteht diese kleine Markierung, die oft nur ein Schatten ist.
Bei dieser Laschenform wird viel mehr Kraft (Druck) benötigt als für die erste Option.
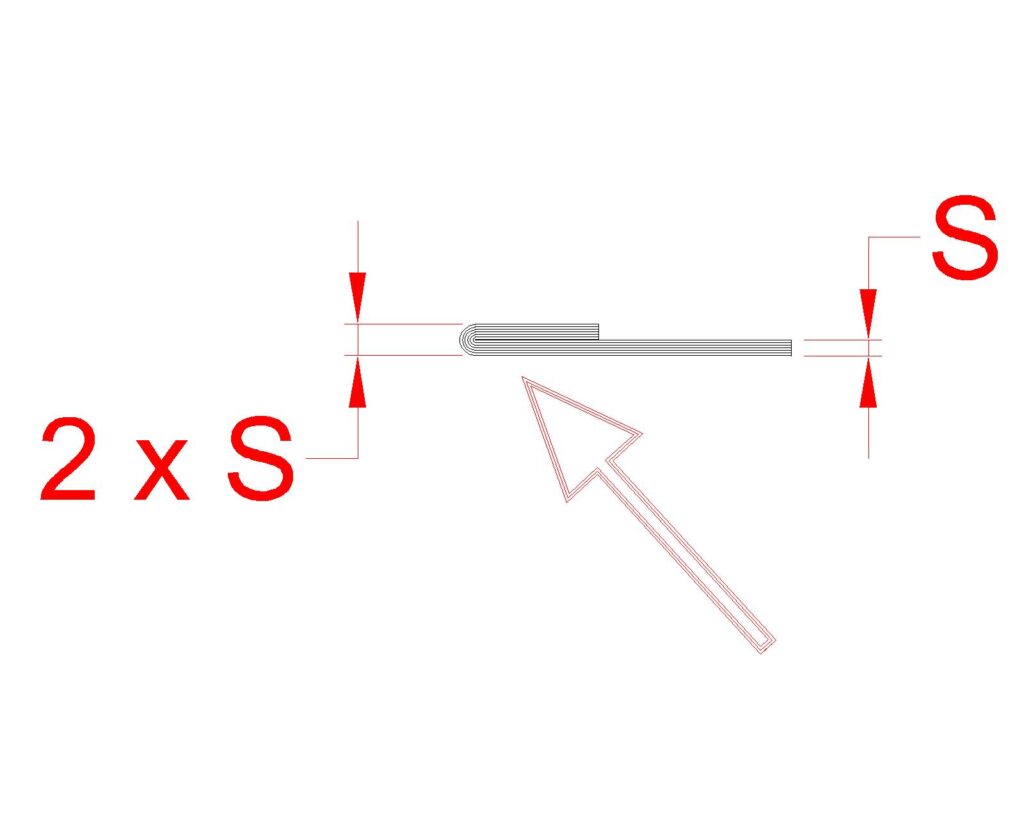
In der folgenden Skizze ist die erforderliche Tonnage zum Anfertigen der beiden Laschentypen zu sehen. Die Berechnung ist vor allem von der Materialstärke und vom Materialtyp abhängig.
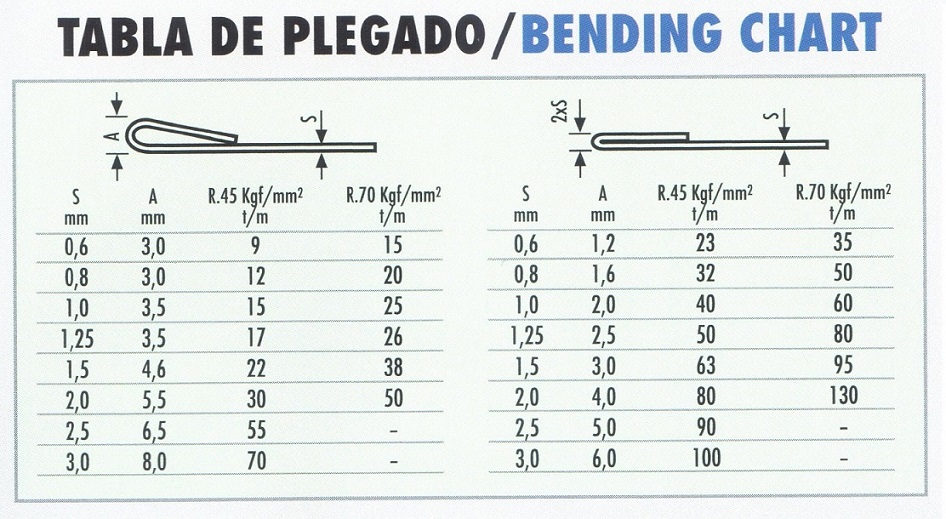
HERSTELLUNGSARTEN VON „LASCHEN“
Die beiden wichtigsten Arten zur Herstellung von „Laschen“ sind die traditionelle Vorgehensweise, d. h. zuerst ein Knick auf 35º und dann ein weiterer Vorgang zum Zusammendrücken, und die zweite Art erfolgt mit den Werkzeugen zum „Bördeln und Zudrücken“, die anhand einer Rückholung über Federn funktionieren.
Wir erläutern die beiden Methoden und ihre jeweiligen Vorteile.
BÖRDELN UND ZUDRÜCKEN IN HERKÖMMLICHER FORM
Wie sich aus der beigefügten Skizze entnehmen lässt, besteht diese Methode aus zwei Teilen. Im ersten Teil wird das Blech auf ca. 35º abgekantet und im zweiten Vorgang erfolgt das Zudrücken.
Es besteht der Nachteil, dass zuerst ein Vorgang durchgeführt werden muss, und danach für den zweiten Vorgang die Werkzeuge der Abkantmaschine ausgetauscht werden müssen, weshalb die Vorgehensweise langsamer ist. Aber die Anschaffung ist üblicherweise etwas günstiger.
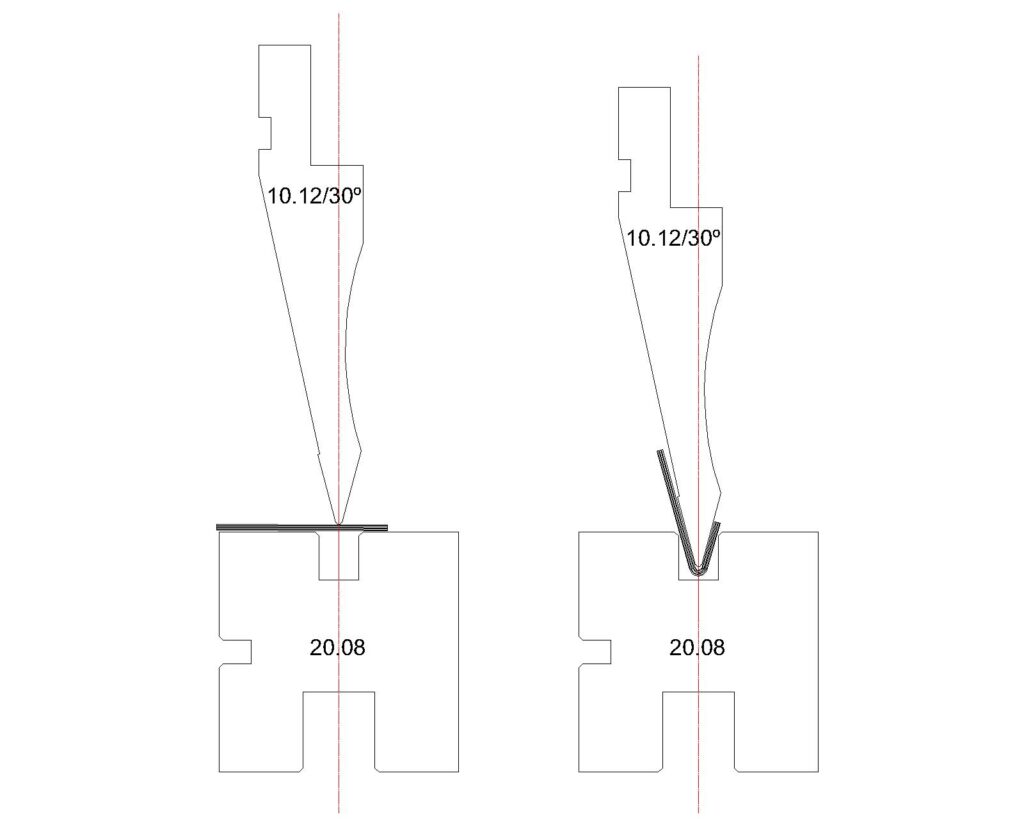
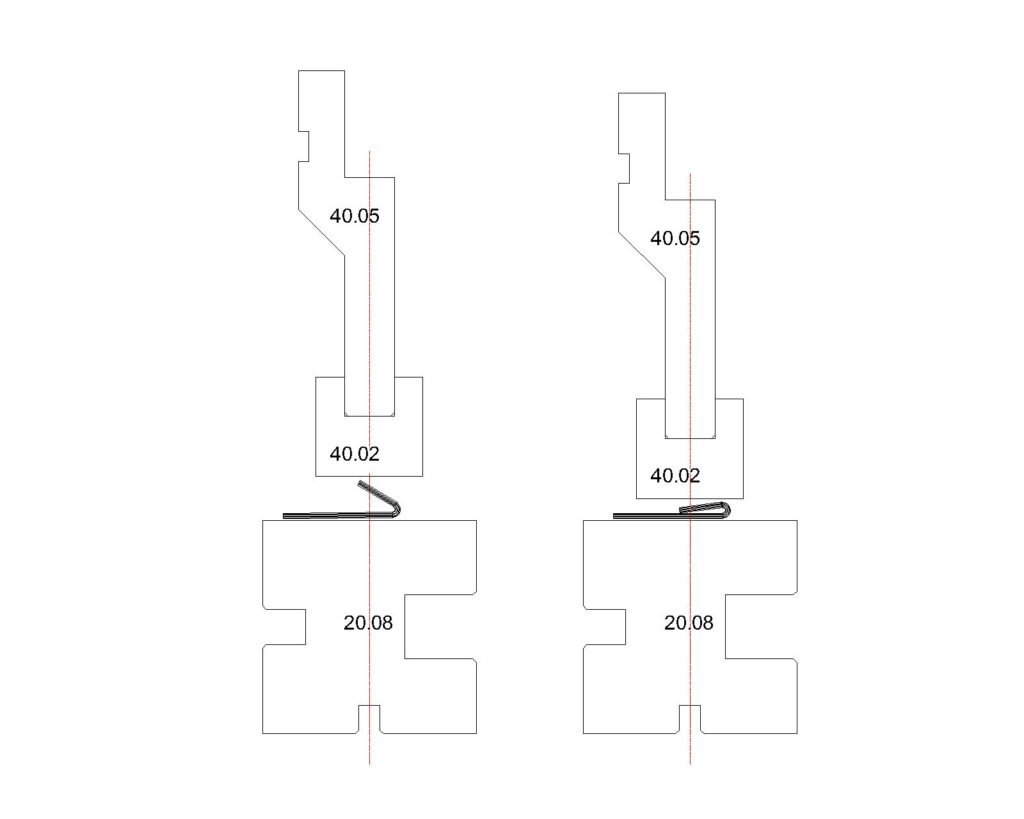
Der erste Teil der beigefügten Simulation wird mit dem Standardoberwerkzeug Mod. 10.12/30º und mit der Matrize Mod. 20.08 durchgeführt, beide aus dem Promecam-System. Der zweite Teil der beigefügten Simulation wird mit dem Oberwerkzeugträger Mod. 40.05 und mit dem Oberwerkzeug Mod. 40.02 sowie mit der Matrize Mod. 20.08 durchgeführt, alle aus dem Promecam-System.
Offensichtlich muss die Matrize eine Matrize mit einem V mit 30º oder 35º sein, aber sie muss auch für die Blechstärke geeignet sein. Siehe Beitrag „Blechabkanttabellen“.
„BÖRDELN UND ZUDRÜCKEN“ MIT STANDARDWERKZEUGEN
Diese zweite Methode lässt sich schneller durchführen, da das Werkstück im Ganzen ohne erforderliche Werkzeugwechsel hergestellt wird. Wie sich aus der beigefügten Skizze entnehmen lässt, besteht diese Methode aus zwei Teilen. Im ersten Teil wird das Blech auf ca. 30º abgekantet und im zweiten Vorgang erfolgt das Zudrücken.
Offensichtlich ist die Anschaffung etwas teurer als die erste Methode, aber wenn mehrere Teile herzustellen sind, ist die Amortisation mehr als gerechtfertigt.
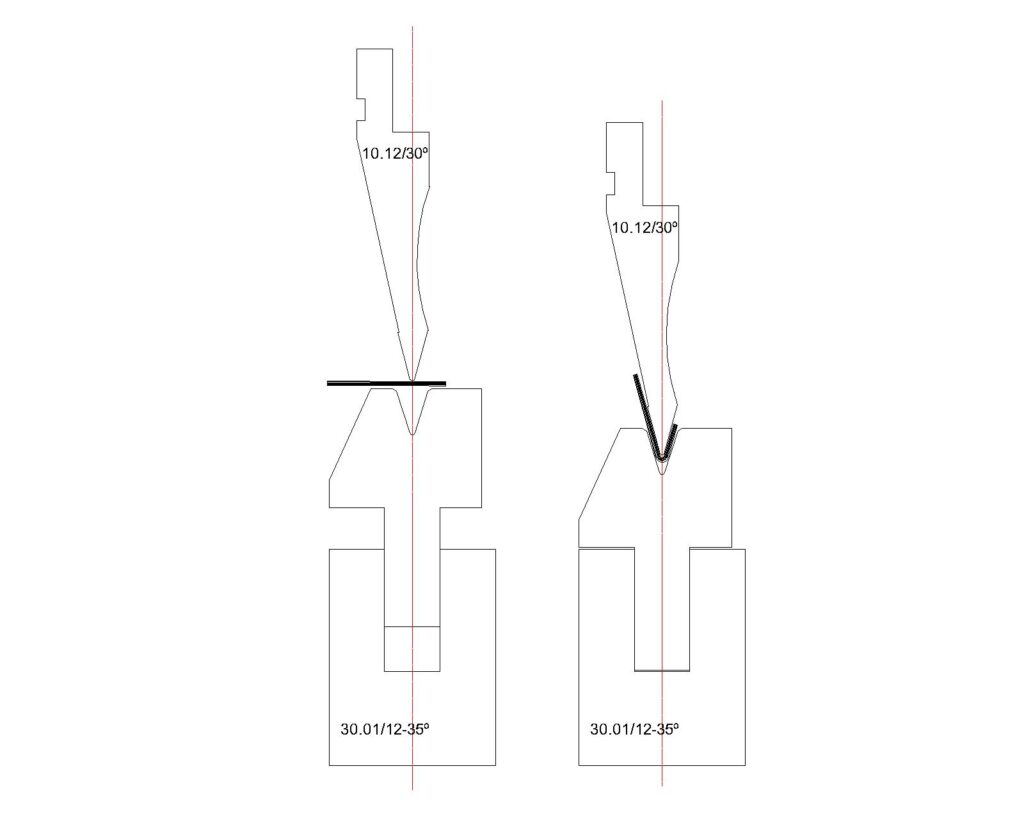

Die Zudrückwerkzeuge zum Bördeln und Zudrücken sind im Inneren mit Federn ausgestattet. Wenn sich die Abkantmaschine zum Abkanten absenkt, geben diese nach. Wenn die Abkantmaschine sich wieder anhebt, dehnen sich diese Federn jedoch aus und das Zudrückwerkzeug kehrt in seine Ursprungsposition zurück. Es gibt auch Zudrückwerkzeuge mit Druckluftbetätigung für anspruchsvollere Kunden, die hohe Produktionszahlen erfordern.
Im ersten Teil der beigefügten Simulation ist zu sehen, wie beim Absenken der Abkantmaschine die Federn nachgeben und das Werkstück auf 30º abgekantet wird. Im zweiten Teil ist zu sehen, dass das auf 30º abgekantete Werkstück an die Stelle des Zudrückwerkzeugs gebracht wird, damit es beim Absenken der Abkantpresse vom gleichen Zudrückwerkzeug zugedrückt wird.
Hier wie auch im vorherigen Abschnitt muss die passende Matrize für die zu verarbeitende Stärke berechnet werden; siehe Beitrag „Blechabkanttabellen“.
EIN VIDEO ALS BESTES BEISPIEL
Im folgenden Video ist zu sehen, wie eine „Lasche“ mit 1-mm-Edelstahl mit der manuellen Methode und dem Oberwerkzeug Mod. 10.12/30º und der Matrize Mod. 20.08 hergestellt wird. Nach dem Austausch der Werkzeuge erfolgt dann das Zusammendrücken mit dem Oberwerkzeugträger Mod. 40.05, dem Oberwerkzeug Mod. 40.02 und der Matrize Mod. 20.08.
Später ist zu sehen, wie eine „Lasche“ ebenfalls an einem 1-mm-Edelstahlblech gefertigt wird, diesmal jedoch mit dem Werkzeug zum „Bördeln und Zudrücken“ Mod. 30.01/35º-V8.
Anhand dieses Vergleichs sind die Vor- und Nachteile jedes Systems einfach ersichtlich und der Benutzer kann das System auswählen, das für ihn besser geeignet ist.